Baseline/GAP analysis provides a true picture of existing practices and identifies gaps against best practices. Following this assessment, the industrial partner and it's C-Suite assembles it's Change Management Team (CMT) having representation from all organizational tiers.


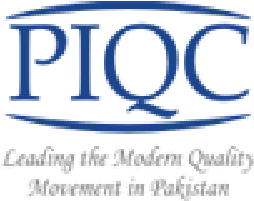

ABOUT DfS
GIZ has been active in Pakistan since 1963, working across three priority areas; Governance, Sustainable Economic development, and Energy. Interventions by GIZ in Pakistan’s textile sector started in August 2014 and subsequently evolved overtime.
The textile and fashion industry plays a key role in modernisation processes and in the transition to an industrial society. It is here that essential entrepreneurial and management skills are developed, which form the basis for diversification of the economy, increase in value added and competitiveness through efficiency gains and technological progress associated with industrialisation.
EVOLVING
FOR
THE BETTER
Change is always good and ‘Dialogue for
Compliance’ evolved from DFC to
‘Dialogue For Sustainability’ after the
environmental component
was added.
This evolution was reflective of the inclusion of all three sustainability pillars:
DfS METHODOLOGY

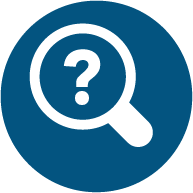
step1.
IDENTIFY PROBLEM

step 2.
CAUSE ANALYSIS

step 3.
GOAL ANALYSIS

step 4.
FIND SOLUTIONS

step 5.
AGREE ON SOLUTIONS

step 6.
ACTION PLAN
HOW DfS WORKS?
Members of the CMT are invited to a two day thematic area CMT workshops
Day one focuses on value added trainings (VATs) on agreed technical topics, day two of each CMT workshop is standardized and dedicated to following the six step approach from problem identification to action planning
In addition to CMTs, regular site visits (mini-CMTs) are conducted with a frequency ranging from once a week to once a month. The purpose of these visits is to monitor implementation and provision of VATs at the factory's shop floor
Post addressing agenda items on the action plan, the engagement comes to an end and with a third party end line assessment

RESULTS & WINS

52%
Average reduction in Worker’s Turnover

31%
Average reduction in Absenteeism

Improvement in two-way communication

46%
Average reduction in order lead time

24%
Average improvement in efficiency

7%
Average reduction in DHUs

61%
Average reduction in machine downtime

45%
Average reduction in work in process

13.4 kWh/kg to 12.8 kWh/kg
Reduction in power consumption per kg of fabric

13.1 kg to 9.7 kg
Reduction in steam production per kg of fabric

163.4 l/kg to 126.8 l/kg
Reduction in water consumption per kg of fabric
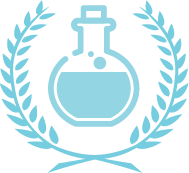
ZDHC has been implemented and appropriate KPIs developed for partner factories
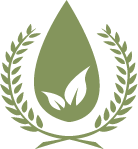
Improved environmental management practices at partner factories including regular EMS risk assessments and other best practices
DfS SUCCESS STORIES
CONSORTIUM
of
DfS PRACTITIONERS
FAQs
-
Lorem ipsum dolor sit amet consectetur adipisicing elit. illum beatae officia quam, accusantium deleniti autem architecto totam deserunt sunt molestias ab.
-
Lorem ipsum dolor sit amet consectetur adipisicing elit. illum beatae officia quam, accusantium deleniti autem architecto totam deserunt sunt molestias ab.
-
Lorem ipsum dolor sit amet consectetur adipisicing elit. illum beatae officia quam, accusantium deleniti autem architecto totam deserunt sunt molestias ab.